Back in summer 2010 I decided that I should return to the “projectile-pusher” approach I used in FANG1. I gave up on this approach far too easily. FANG1 worked, but was unreliable. When I started planning FANG2 I considered the unreliability to be inherent to the projectile-pusher design and that nothing could be done about it.
Now I will systematically go through all of the problems I can recall and propose solutions.
Pinching of the darts in the breech
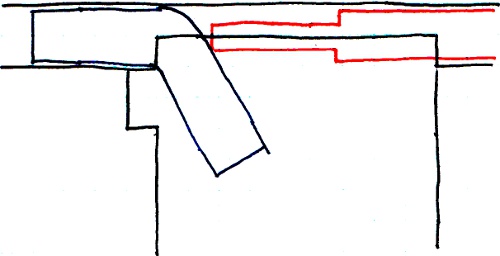
Darts could be simultaneously in the breech and the magazine. This seems to have been caused by the darts buckling which caused the dart back end to pop out of the breech and go into the magazine.
Potential solutions:
- Reduce the dart length. The critical bucking force depends strongly on the length of the dart. The darts I used in FANG1 were atypically long at 2″ anyway, so this would make my darts closer to typical darts.
- Add a flow control valve before the pilot valve. The problem may be caused by the bolt moving too fast for the dart to move, causing the buckling as one end wants to move but the other wants to stay. Slowing down the speed of the air cylinder is one way to solve this problem. Note that the flow control valve must go before the pilot valve in the air circuit as this is the only location that will not impact performance when firing.
- Reduce the force applied by the air cylinder. There are two ways to do this. Either the pressure could be reduced or the diameter of the air cylinder could be reduced.
- Have a tapered dart entrance. This would make one end being stuck more difficult.
- Have a domed dart head. This would make one end entering the breech easier.
- Use a larger diameter foam. This would increase the critical buckling force, however, it is not practical as the vast majority of darts have a diameter of about 0.53 inches.
- Increasing the friction coefficient of the back of the dart or the front end of the bolt. This would allow for the bolt to grip the top of the dart better, hopefully making the dart popping out from buckling more difficult and/or changing the effective length factor.
- Add a spike to the front end of the bolt. This would allow the darts to be impaled, immobilizing them such that they can’t pop and and be pinched. However, this has several distinct disadvantages:
- Could potentially cause harm if fingers/other body parts are caught in the breech area.
- Might impale the wrong part of the dart, decreasing reliability.
- Holes in the back of the dart could accumulate, eventually making them incapable of being impaled.
- Impaling might have a negative effect on performance if it makes the equivalent static friction too high. However, this might also increase performance.
Darts get caught in the empty space between the magazine side and bolt tube
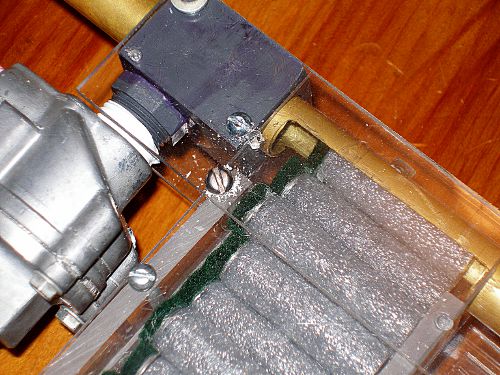
This problem is not shown in the photo above, but the problem’s cause can be seen. When the bolt moves forward and a dart is pushed into the breech, often friction pulls another dart into the space between the bolt tube. When the bolt retracts, this dart most often is also pulled back, but this does not always happen.
The actual problem is shown in an approximate drawing below.
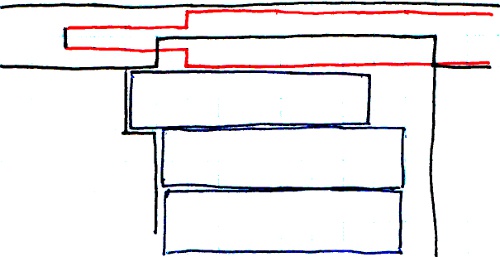
The solution to this problem is simple: Ensure that both sides of the magazine are smooth up until the dart entry point. (I want both sides to be smooth to prevent this from occurring on the other side of the magazine.)
Darts get caught on the threads from the bolt
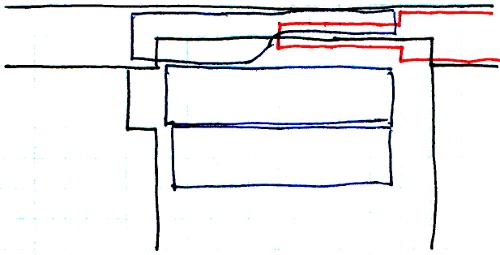
Rarely the darts would buckle in the opposite direction as they did when they were pinched between the bolt and the tube. They’d be caught between the threads of the front part of the bolt (visible in this image in the center) and the bolt tube. The darts would be stuck here until they were cleared by hand, usually, as I recall.
Unfortunately, it seems that I have lost my photos of the construction of FANG1, but a few photos I put online are still available, hence the link to the image above.
One solution to this problem is to make that part of the bolt smooth. Another solution is to increase the diameter of that part. Unfortunately, that leads to flow restrictions. Yet another solution might involve extending the wider part of the bolt and having a flow path through the solid bolt. And yet another solution is to shorten that part, which will make the dart more likely to be freed because it can not go as deep. Likely, I will only be able to make the problem part smooth and reduce the length of the extension, and hopefully this will be adequate.
Bolt does not return
Sometimes the bolt would not return. This was caused by a weak return spring and excess friction in the bolt. Some obvious solutions include making the return spring stronger and lubricating the bolt.
I may use an air spring in FANG4 for the return. This would allow me to have full control over the return force.
Darts can feed at the wrong angle
The magazine follower wasn’t made correctly so that darts could feed in at the wrong angle. If the follower was made a little wider, this would not have been a problem.
Jams can’t easily be cleared
When FANG1 jammed, I often would have to disassemble part of the gun to remove the jam if it could not be cleared by cycling the gun a few times. Easy access to the bolt area is necessary to clear the jams, as is some sort of switch to ensure that the bolt is retracted.
Barrel can be dented
FANG1 used unexposed brass. This is prone to being dented, and the dents could affect seal or cause the bolt to lock up. Some sort of sleeve around the brass where used is necessary. Replacement of brass where it does not need to be used (like in the barrel) with a stronger material like aluminum (the available aluminum barrels are far thicker) also avoids this problem.
Many sizes of brass are used
In FANG1 I used four different sizes of brass. One was for the bolt, one was for the barrel, and the other two were there because I didn’t have a 9/16″ drill bit. These two are not necessary at all. They only increase cost and weight. They can be removed if I get a 9/16″ drill bit or use someone else’s machine shop.
The barrel assembly leaks
As I did not seal the barrel assembly in any fashion, there probably were non-negligible leaks. Sealing the barrel assembly with something like epoxy or O-rings would be desirable.
Difficulty loading
Loading the magazine was fairly difficult as FANG1 never was intended to be a practical blaster. I’d have to pull on a string to move the follower down and then manually insert darts into the magazine. I’d like to replace the string with a piece of metal much like BS-9 and add some sort of locking mechanism to keep it open while loading.
I should also pay attention to make loading darts correctly as easy as possible. Loading darts incorrectly was very easy with FANG1. I’m not quite sure how to do this, but I’ll give it some thought.
These are the main problems with the performance and functionality of FANG1 that I intend to address in FANG4. There are many other problems, most of which stem from a lack of features. For example, FANG1 did not have a pump, which I now consider to be a problem. FANG1 also had a rather primitive magazine system; I still intend to use an internal magazine, but I want to make it more robust. I may detail these other improvements and changes in a future post.